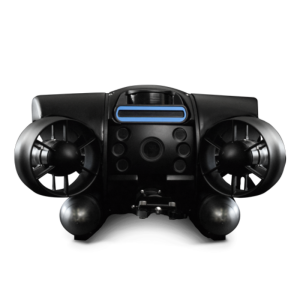
Foss Maritime and Amanda Dayton
We were delighted to speak to Amanda Dayton of Foss Maritime. The Seattle Shipyard’s Manager of Contracts and Estimating, Amanda is a driven, ambitious, organized, conscientious engineer with 15 years of detailed engineering experience in marine design, new construction and vessel repair and modifications. She joined Foss Maritime’s engineering department, the Harbor Marine Group, in June of 2016 and is currently onsite at the Foss Seattle Shipyard supporting new construction, conversion and repair projects. She is also implementing marine field robotic equipment, including 3D laser and optical scanning and ROV operations. Prior to her employment at Foss, Amanda served as Project Engineer for the Arctic Challenger conversion in support of Shell’s Arctic Drilling Program, provided engineering support for 12 new construction vessels and several modification projects at Dakota Creek Industries shipyard and completed numerous design and engineering assignments at Elliott Bay Design Group. She has her Bachelor’s and Master’s Degrees in Naval Architecture and Marine Engineering from the University of Michigan and is currently earning her second Master’s Degree in Unmanned Systems from Embry Riddle Aeronautical University. She completed her Fundamentals of
We were delighted to speak to Amanda Dayton of Foss Maritime. The Seattle Shipyard’s Manager of Contracts and Estimating, Amanda is a driven, ambitious, organized, conscientious engineer with 15 years of detailed engineering experience in marine design, new construction and vessel repair and modifications. She joined Foss Maritime’s engineering department, the Harbor Marine Group, in June of 2016 and is currently onsite at the Foss Seattle Shipyard supporting new construction, conversion and repair projects. She is also implementing marine field robotic equipment, including 3D laser and optical scanning and ROV operations. Prior to her employment at Foss, Amanda served as Project Engineer for the Arctic Challenger conversion in support of Shell’s Arctic Drilling Program, provided engineering support for 12 new construction vessels and several modification projects at Dakota Creek Industries shipyard and completed numerous design and engineering assignments at Elliott Bay Design Group. She has her Bachelor’s and Master’s Degrees in Naval Architecture and Marine Engineering from the University of Michigan and is currently earning her second Master’s Degree in Unmanned Systems from Embry Riddle Aeronautical University. She completed her Fundamentals of Engineering (EIT) Exam in October 2004 and will sit for her Professional Engineering (PE) exam in April 2020.
TELL US ABOUT FOSS MARITIME AND HOW YOU ARE USING THE ROV
Foss Maritime Company is based in Seattle, WA, and offers a complete range of maritime transportation and logistics services. Along with its independent subsidiaries, Foss maintains a fleet of hundreds of tugs and barges throughout the United States. Foss is recognized for its state-of-the-art vessels, experienced and dedicated crews, knowledgeable customer service staff and world-class engineers. In addition to transportation and maritime logistics, Foss also provides engineering and shipbuilding services to assist customers throughout the entire life cycle of a project including analyzing vessel and equipment requirements for a specific job, to designing a new build or vessel modification through to production and proper outfitting of a vessel.
The Foss Shipyard encourages employees to focus on continuous improvement and business development opportunities. As part of an approved Continuous Improvement Initiative, Foss purchased a DeepTrekker ROV in order to reduce the costs of using divers for diagnosis of damage response and equipment failure inspections, blocking/pre-drydocking checks, pre-operation/charter vessel surveys, quality assurance information among other potential options such as UWILD external specialist certification for basic barge inspections. The predicted savings was $68,500 for the first year and $87,500 annually thereafter. However, after tracking the first year of ROV use, Foss realized an astounding actual and measurable impact of saving/earnings of a total of $135,650, which was DOUBLE original predictions (not including immeasurable costs such as losing a tow job due to waiting on divers or potential cost of increased equipment damage due to inadequate underwater information).
WHAT DOES YOUR DAY TO DAY WORK WITH THE ROV CONSIST OF?
The Foss Shipyard began to use the ROV on almost a weekly basis, whether it was called in to perform block checks during a drydocking, inspecting the hull and running gear of moored vessels coming off-hire or ramping up for work, or providing helpful information on equipment failure. The ROV was light enough to be manually carried from pier-to-pier or office-to-pier by one person and did not require a shorepower connection so it was easy to transport to the vessel location, which is important when dealing with working vessels. The ROV operator would fill out a Job Safety Analysis form and a Pre-Dive survey before operating the ROV to ensure operational safety and awareness before beginning an inspection. The operator would then splash the ROV as close as possible to the vessel inspection site and work with the dockmaster or vessel owner to ensure proper inspection and that photo and video data was captured for reporting purposes. The ROV is easy to handle and lift in and out of the water. Once the inspection was complete the ROV operator would bring the vehicle back into the office for storage and battery charging then download the data to a computer and develop a dive report noting hull and equipment condition and pointing to any irregularities. The report was then emailed to interested parties. Then I would work on my other estimating duties! Occasionally the tether can become pinched on hull appendages or other underwater obstructions, but the vehicle is small and maneuverable enough to be able to redeem itself from such situations. The size is also handy to maneuver into tight spots for detailed inspections.
WHAT CHALLENGES WERE YOU TRYING TO SOLVE WITH THE ROV?
In addition to alleviating diver costs, Foss also notes that external vendors can impact overall project timelines due to our dependence on fitting into their schedules of availability and also having to wait until the dive team can all organize themselves to the same time and place. Also, due to safety concerns of having divers in the water, sometimes there are delays to ensure that the vessel is in a condition that is stable and safe enough for dive operations. Since the ROV can be operated by one person, it is deployed MUCH faster than divers and has way more schedule flexibility as well as operational flexibility since diver health is not a concern.
WHAT MADE DEEP TREKKER STAND OUT TO YOU AS AN ROV THAT WOULD BE BENEFICIAL FOR SHIP HULL INSPECTIONS? HOW DID YOU DECIDE THAT THE DEEP TREKKER WOULD BE AN ASSET FOR YOUR WORK?
The marine industry can be quite risk adverse to investing in new technology so honestly the deciding factor was the low purchase and lifecycle cost of the ROV. There was a huge potential for payoff with a low buy in. We would only have to use the ROV twice instead of calling divers in order to realize a return-on-investment. We also appreciated the simple and waterproof design so that if anything broke or needed maintenance, it would not be a financial burden or disable it from service for very long. We decided that the ROV was an asset for our work by analyzing our yearly diver costs versus the cost of investing in the purchase, operation and maintenance of the ROV.
ARE THERE SPECIFIC FEATURES OF THE ROV THAT YOU FIND MOST USEFUL FOR SHIP HULL INSPECTIONS?
The specific features that we found most useful were first the low cost of the ROV, then the small size and the light weight for transportation and deployment, the ability to capture photos & video with DVR, the ease of operation (not too many buttons or extra equipment or confusing features), the neutrally buoyant tether (we use it to find the way back to the operator! It’s easy to get lost underwater!), and the quick operational speed and maneuverability. DeepTrekker specifically has also been particularly wonderful with their sales and customer service team!
HOW DID YOU CONDUCT SHIP HULL INSPECTIONS BEFORE YOU HAD THE ROV?
We used divers and only minimally because of the cost. We have used the ROV way more than anticipated due to how easy it is to transport and deploy and it has saved the company a lot of money, in one case even to verify that divers were needed when there was reluctance to call them!
HAVE YOU MADE ANY INTERESTING DISCOVERIES WHILE USING THE ROV?
The biggest surprise to me was how extremely skeptical co-workers and customers were at first with we used the ROV and how quickly their minds changed to solid believers after witnessing a couple jobs.
WHAT MADE YOU HAPPIEST ABOUT WORKING WITH THE DEEP TREKKER?
I love seeing the posts on the Deep Trekker social media sites of the ROV’s in use. And as I mentioned earlier, I have been extremely satisfied with their sales and customer service. I receive prompt and thorough replies as well as follow up. ROV’s are such a fantastic tool for the marine industry and I am so excited for their potential as they become more capable. I have presented at a number of professional societies touting its use for vessel owners and representatives as well as shipyards. I hope that more and more companies see the advantages for their use and make the investment because I know they would be ecstatic with the results! I am quite passionate about leveraging robotic technology so I love this opportunity to talk about my experience and further spread ROV ideas through the marine industry.
We want to thank Amanda Dayton for her time in answering our questions! As always, you can reach out to our industry experts for more information.
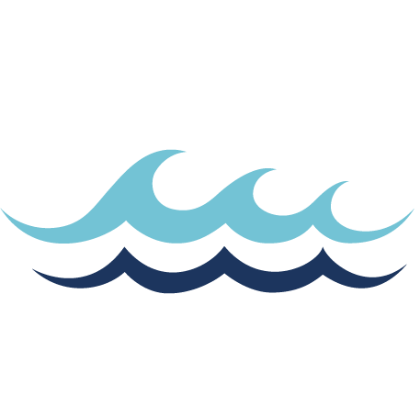