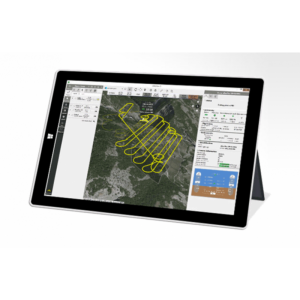
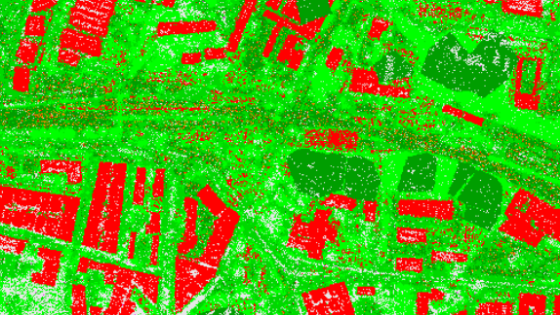
Corridor Mapping in Turkey Using Drones versus Traditional Instruments
Awarded the Turkish government’s first UAV survey contract, Artu Harita used a senseFly eBee to map a huge 140 km-long rail corridor. The quality and quick turnaround of the company’s data products impressed its client and outperformed its traditional surveying counterparts.
When Turkish State Railways needed to conduct a full land survey of a proposed high-speed rail route, due to connecting the capital Ankara with İzmir, its engineering department divided the route into three roughly equal sections. Survey contracts were then awarded to three separate providers in order to minimise project risk, comply with Turkish bidding law, and compare results.
Two suppliers would use traditional terrestrial surveying techniques, such as GPS base stations and total stations, to survey their corridor segments. For the third westernmost segment, however, the government’s team chose a different approach, employing engineering services company Artu Harita to source point data from the sky using its senseFly eBee mapping drone. “In the past, the client’s aerial data was collected by photogrammetric flights made by real planes, but for this project the rail authority specified UAVs,” explains Diner Yılmaz, General Director of Artu Harita. “Its team specified the resolution required, which was 15 cm per pixel (we achieved 10 cm), and ten of their engineers also went into the field and took points, which they used to check our full data set.” The corridor segment that Yılmaz’s team was contracted to map, connecting Manisa with Uşak, measured 140 km (87 miles) long by 600 m (1,968 ft) wide, a huge undertaking with a total survey area of 11,000 hectares (over 27,000 acres).
“We surveyed plains, hills, mountains and urban areas, over two months, in all types of weather,” Yılmaz says. “With classical techniques, you just couldn’t map the areas we did. The mountain areas at the eastern end of our region, for example, you can’t reach, either by car or even sometimes by walking. With the photographs the eBee captured, our engineers then produced a whole range of data products.”
The client’s main need was for a large vectorised data set. The classified point cloud Yılmaz’s team created would enable the client to easily identify and measure buildings, roads, street lights, power lines, vegetation, old and existing railway lines, altitude points and more. “In Turkey, vectorisation is everything,” Yılmaz notes, “especially because we don’t have a national GIS system we can use to integrate or add to past data.”
UAVs vs classical surveying
Yılmaz adds that, in his experience, the pure amount of useable data a drone can collect clearly sets it apart from classical surveying techniques. “This comparison depends on the manpower you have of course – you might have ten or twelve people – but you need all the GPS equipment too,” he says. “You might get a 5 metre, 10 metres or 20-metre grid, but with eBee, we have a point cloud with an average grid of about 20 cm. For a site of 100 hectares, with a classical system, you might measure 30,000 points. With the eBee, we’re talking about 25 million points. So with the drone, we can show the terrain more smoothly and see everything, the trees, the rocks, in much more detail.” The data turnaround time achievable with UAVs is also a key benefit, Yılmaz says: “Using classical methods we need lots of people, lots of time, and lots of surveying instruments. With the eBee, we just need people to paint and set ground control points, and people to fly the drone. For this job, we had just four people in the field, plus four or five freelancers to help set GCPs.''
Drone benefits
Yılmaz and his team are no strangers to capturing point data via drone, having used their eBee for 22 projects in the past 15 months alone, a total of 200 flight hours spanning 90 flights. “We’ve used our UAV for many different projects: mapping, road and railway projects, power lines, dam and construction projects, renewable energy and more. For us, this product is the perfect intersection of user-friendliness, quality, price, support, and software,” Yılmaz says. A big drone plus, Yılmaz says, is the altitude at which such systems fly: “This is much lower than real planes so we don’t feel the effects of cloud, which is normally at 1 km altitude. For this rail project, for example, we flew at just over 300 metres. This flexibility is important because sometimes we already had a small flight window due to the climate.”
Drone methodology
Yılmaz used the eBee’s eMotion software to plan each flight, dividing the 140 km-long corridors into 16 km segments and choosing a take-off point at the centre of each. The drone’s operators would then arrive at this point and fly first in one direction (i.e. 8 km out to one end of the segment and back), then carry out another ‘there and back’ flight to the parcel’s opposite end. “This flight planning was a little more complicated than setting rectangular or polygonal coverage areas in eMotion, which is the normal way. Instead, we had to manually create the flight lines, which took a little longer,” Yılmaz says.
This eMotion flight plan spans the western half of one 16 km corridor segment. Yellow lines show the flight’s ‘8 km there, 8 km back’ trajectory, green lines show the corridor’s perimeter, and the faint grey line in the centre is the proposed rail line. Yılmaz specified a required ground resolution in eMotion of 10 cm per pixel, basing this choice on his experience of what the eBee could achieve, rather than specifying the lower resolution of 15 cm/pixel that the client required. eMotion then automatically calculated a flight altitude of approximately 320 m above the drone’s take-off point, the eBee collecting an average of 300 photos per flight (9,000 in total over the project’s 30 flights). While one, or occasionally two staff would plan and fly the drone’s flights, Yılmaz’s other three field engineers, along with several local freelancers, were divided into two teams, responsible for setting the ground control points (GCPs) required to geo-reference the drone’s images.
The first team of four would typically be positioned 20-30 km ahead of the drone, while the freelance team might work another 20- 30 kilometres beyond that. However once the project had begun, Yılmaz soon realised that the single line of GCPs he had envisaged, running along the proposed rail line, would not be enough. “We set a minimum lateral image overlap of 50% and a minimum forward overlap of 80% in eMotion, but aligning the images correctly was still a challenge; it was hard to align photos due to the width of the corridor. So we set two extra lines of ground control points; one towards each edge of the survey area,” he notes. “This allowed each image to be ‘fixed’ in place, whichever side of the rail line the drone was flying, by using at least one GCP from the central route line, and one from Approximately 900 GCPs were set in total. 500 of these were registered with the client, with the remaining 400 used to improve the quality of the results. “When our field guys were setting their GCPs, they were taking checkpoint measurements too, between one GCP and the next, aiming for a homogenous distribution,” Yılmaz claims. “We would measure each GCP somewhere between 15 epochs and two hours, but our checkpoints didn’t need such precision so we usually measured for just 1-2 epochs. All randomly selected points. When aligning our polygons we then used the government’s very precise, solid polygons, which the authority made using 1-2 day GPS sessions. Those points were our starting point.” Artu Harita’s team of four spent 60 days in the field, including 20 flying days.
The images the eBee captured were continually transferred back to the office for processing, with 10 engineers dedicated to processing and creating the final data products. “They handled everything from the image processing through to analysis, point cloud classification (a mix of manual and automatic processes), and turning the ground data set into digital models and different types of drawings,” Yılmaz explains. “This part took around 40 days.”
Results
From the project’s kickoff to the final delivery of the client’s products took three months. “The companies the authority used to survey the other two sections, using classical techniques, took up to a year each. And because they were taking manual senseFly is a Parrot company. Copyright © senseFly 2015. All rights reserved. senseFly Ltd., 1033 Cheseaux-Lausanne, Switzerland. 4 GPS measurements on the ground, working manually, they PROJECT STATISTICS couldn’t give the client orthophotos, and their point cloud and vector data was not as detailed as ours,” Yılmaz states. “With the eBee, we achieved an average accuracy of 10-15 cm,” he adds, within the typical range of one to three times GSD and better than the project’s goal of plus/minus 20 cm. “The authority actually told us they preferred our data and they wished they had made the entire project with UAVs.”
About Artu Harita
Founded in 2012 by Ergün Mumcu and Hakan Uygur, Artu Harita Bilişim GIS Mühendislik (www.artuharita.com.tr) is a geomatics engineering company based in Ankara, Turkey. “Our most common projects are mapping, GIS and IT jobs, for example, covering remote sensing, data analysis and building software for GIS systems,” explains General Director, Diner Yılmaz, who joined in 2013. The company’s staff comprises survey engineers and IT engineers, ten of whom are office-based, with another six working in the field.
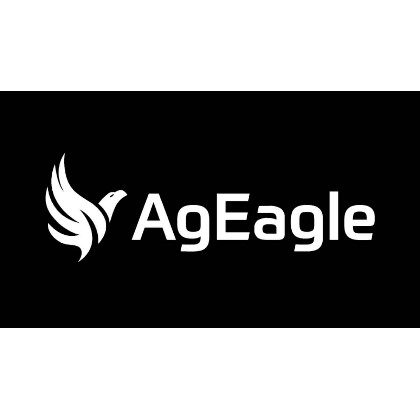
Related products
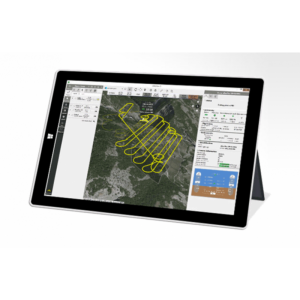